Blog
Case study: Field experience with heat exchangers operating long periods of time in extremely harsh environments
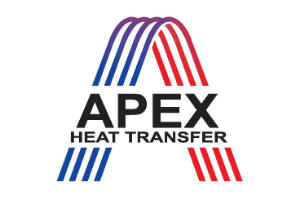
Read also: Special Report: Burckhardt Compression About Gas Compression SystemsAPEX Group is specialized in designing and manufacturing heavy-duty plate-type and tubular Heat Exchangers (see Fig. 1) for handling large volumes of gases for heat recovery and gas treatment applications. The operation principle consists in passing cold gases (e.g. air) and hot process gases (e.g. flue gas) through alternating parallel channels in cross or countercurrent arrangement.
In the case study, the operation was shut down on an annual basis due to the constant plugging of the heat exchanger. A careful analysis and implementation of an adequate maintenance cycle helped to increase the continuous operating time of the heat exchanger.
After the replacement of the heat exchanger, we studied the effect of the particulates on our heat exchangers. The case study resulted in an improved design, as shall be demonstrated in our presentation. Join us on PRC Europe 2020 to find out more.
Additional options for you:
- find out more about Petrochemical and Refining Congress: Europe at prceurope.com
- request marketing materials here
- share the article in social networks using the buttons below